Waste Electrical and Electronic Equipment (WEEE) is one of the fastest growing waste types [1]: with three times higher growth than municipal solid waste [2]. Electrical and Electronic Equipment (EEE) industry consumes 30% of annual silver (Ag) production (6,000 t), 12% of gold (Au) (300 t), 15% of bismuth (Bi) (900 t), 19% of cobalt (Co) (11,000 t), 30% of copper (Cu) (4,500,000 t), 14% of palladium (Pd) (33 t), 50% of antimony (Sb) (65,000 t) and 33% of tin (Sn) (90,000 t) manufacture [3]. A large quantity of WEEE is traded illegally, and in 2011 only the legal trade of WEEE was estimated at 52 billion USD [4]. Common discarding of waste in landfills or open spaces, is highly damaging to the environment [5]. Despite the efforts to limit illegal waste streams by a legal framework, approximately 70% of WEEE in the world is discarded in China [6], together with Waste Printed Circuit Boards (WPCBs). WPCBs form an integral part of Electrical and Electronic (EE) equipment and account for 3-7% [7], [8] of its mass. The average annual increase in Printed Circuit Boards (PCB) production is 8.7% [9]. More than 1,000 substances [10] and up to 54 different metals [11], are present in PCBs but the separation of valuable metals, particularly Au and Cu, is generally the main goal of their end-of-life treatment. Treating WPCBs is a particularly complex process due to the dynamics of their development, use of new materials with the aim of reducing components and a more rational use of raw materials. PCB waste treatment requires a huge amount of human work, together with methods and chemicals that are potentially hazardous for the environment [12]. When an electronic product is disposed of and its recovery is carried out by manual separation, it is mostly PCBs that are separated as they represent the only fraction of WEEE whose recovery is economically justified [13]. There is a range of methods used for a PCB recovery. However, despite that, up to 30% of metals are not recovered with the treatment methods used in China [14].
WEEE management system should be based on a material flow management [15], wherein WEEE is not a type of waste but an anthropogenic stock of materials [16]. Currently, there is a general trend towards recycling [17], that is, a recovery of valuable materials from PCBs, and disposal of the remaining part [18]. PCBs are treated using pyrometallurgical, hydrometallurgical or mechanical processes [19]. The most frequent reason for a WPCBs treatment is the separation of Au and Cu. The indirect benefit of a WPCB recovery is achieved by saving energy necessary to produce metals from primary raw materials, with simultaneous reduction of emissions into the air and toxicity of residues. In the available literature, there is little information on the proportion of metals in certain classes of crushed samples of WPCBs [20]. A list for prioritizing metal recovery for end-of-life PCBs was composed by Wang and Gaustad [21] considering the market value of metals, ecotoxicity and the possibility of energy saving through recovery treatments.
The published results on the metal content in WPCBs presented in Table 1 show very diverse data [22].
Contents of nine metals in WPCBs according to the results published so far in literature given above
Metal | Number of data | Mean* (X̄) [%] | Min. share[%] | Max. share [%] | Standard Deviation*(SD) [%] | Coefficient of Variation* (CV) [%] | Share inores* [%] |
---|---|---|---|---|---|---|---|
Al | 40 | 4.06 | 0.26 | 13.50 | 3.00 | 73.87 | 30.00 |
Cu | 52 | 19.10 | 3.00 | 37.81 | 9.17 | 48.01 | 0.50-3.00 |
Ni | 41 | 0.95 | 0.00 | 5.35 | 1.02 | 107.05 | 0.70-2.00 |
Pb | 43 | 2.84 | 0.80 | 15.48 | 3.48 | 122.62 | 0.30-7.50 |
Sn | 35 | 3.25 | 0.62 | 8.83 | 1.90 | 58.38 | 0.20-0.85 |
Zn | 37 | 1.50 | 0.04 | 5.92 | 1.30 | 86.88 | 1.70-6.40 |
Ag | 47 | 0.1027 | 0.0000 | 0.3800 | 0.1098 | 106.9579 | 0.0005 |
Au | 47 | 0.0290 | 0.0000 | 0.1500 | 0.0357 | 123.2660 | 0.0005 |
Pd | 28 | 0.0186 | 0.0010 | 0.0680 | 0.0178 | 96.0849 | no data |
Supplemented data from [23]
The starting point for defining any waste treatment method is knowing specific waste composition and waste quantities, because selected treatment technology depends on it. This paper presents data on the content of essential metals in WPCBs collected in a typical developing country that are necessary for the exploitation of valuable metals and for the reduction of the toxicity of the residue. The differences in the determined metal content, among other reasons, can be attributed to the age of the equipment, as well as to the time when testing was carried out and to the sampling area. The age of the equipment (i.e. the age of WPCBs for the observed period) was determined by the time when testing was carried out and by the life span of EEE as a particular feature of economic and social circumstances in an observed area/country. That means that the age and life span of EEE in developed and developing countries differ substantially. Therefore, a high dispersion among the published data in Table 1 was not surprising. Several authors analysed only certain types of WPCBs (non-uniform sampling), while the others used PCB samples directly from the production process, or from similar situations.
The research presented in this paper determines the metal content of WPCBs in everyday devices we most frequently use such as cell phones, TV sets, and computers both for electronic components and bare WPCB base plates. The research also considers the metal content in relation to different grain sizes, i.e.: 1-4 mm, 0.5-1 mm, 0.1-0.5 mm and < 0.1 mm. WPCB samples were collected in the Republic of Croatia, a new EU member, as an example of a typical transition country.
Figure 1 shows that the global economic crisis, which started in 2008, had its effect on the Republic of Croatia, since a decreased quantity of EEE was traded on the market during that period. On the other hand, during the first several years of the crisis, a significant progress was made in the collection of WEEE, followed by several years of stagnation and a slight decline. The collection of WEEE increased in 2015 again. The annual amount of WEEE collected increased four times during the observed period (2008-2015), from approximately 1.3 to 5.5 kg/per capita. It can also be noticed that almost all the waste collected was treated (recycled). Approximately 50,490 t of EEE was traded on the Croatian market in 2016, compared to 38,815 t (76.87%) of WEEE which was collected. WPCBs were separated and sorted manually to recover metals like Cu and Al, and the remaining part was sent for further treatment.
WEEE management in the Republic of Croatia [24]
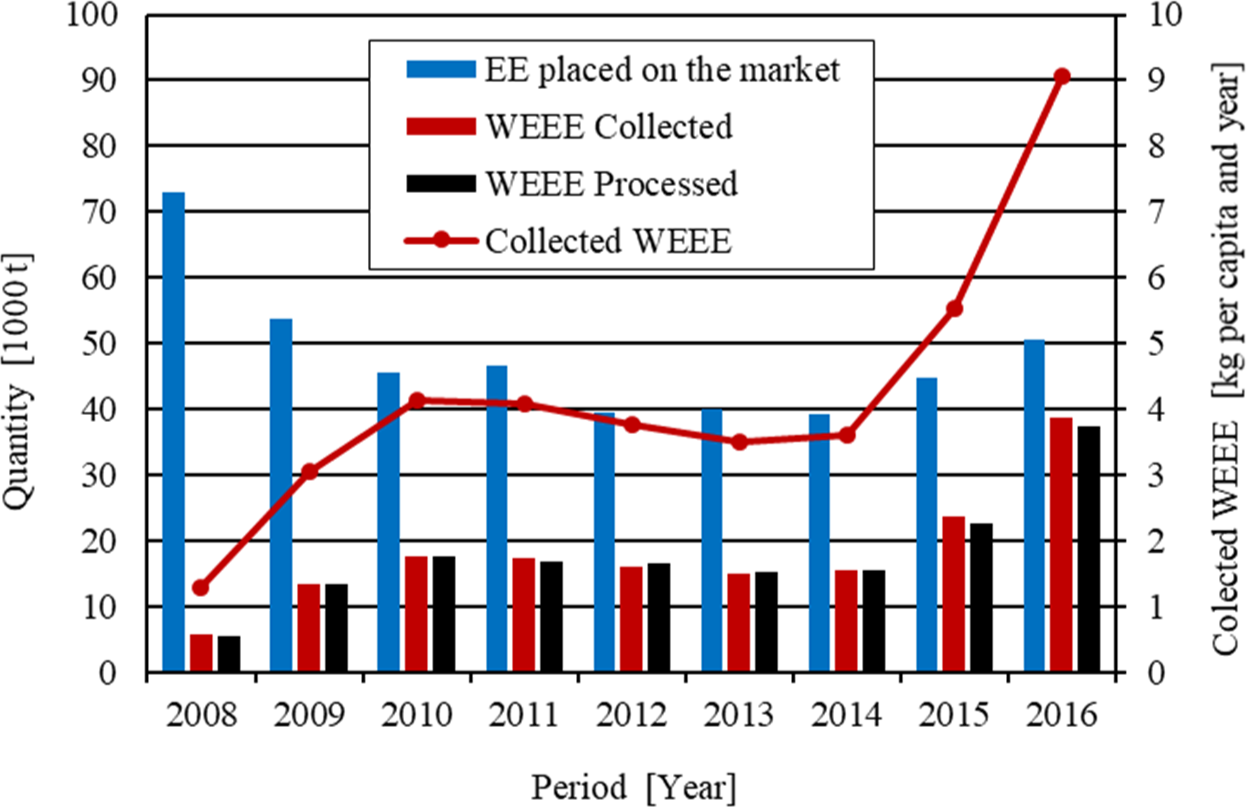
The selection of samples was adapted to the European WPCBs market, and the grinding methods and obtained classes, into which samples are divided for a more detailed testing, were adapted to the improvement of the existing WPCBs processing technology in the Republic of Croatia.
The subject of the research presented in the paper are WPCBs from WEEE collected in the Republic of Croatia. Sampling was carried out in cooperation with Spectra Media Ltd, the only company authorised for the treatment of the 2nd to 10th category of WEEE in the Republic of Croatia. Seven samples of WPCBs separated from WEEE of different age were selected from bags containing manually separated and sorted WPCBs. The average mass of an individual sample was 28 kg.
A so-called CPOLD label was used for PCBs from Cell Phones (CP) of an older generation and a defined CPNEW label for a newer generation (smartphones manufactured after 2008). Another COLD label was used for PCBs separated from computers with a Pentium 4 processor or older (i.e. single-core) processors, while in addition a CNEW label was used for the PCBs from computers with newer processors. The PCBs from TV sets were divided into three categories. The first category had a CRT label that was used for PCBs from older models of TV sets with a Cathode Ray Tube (CRT). The other two categories of PCBs were from newer models of TV sets with Liquid Crystal Display (LCD) technology. The category marked with LCDCSP was used for PCBs used for computer signal processing, and a category labelled with LCDSR referred to PCBs used for signal reception.
The testing procedure is presented in a schematic diagram displayed in Figure 2, and further described in detail in the following text. The electronic components of WPCBs were dismantled manually from base plates using hot air in all the samples except WPCBs from cell phones (CP samples). It was not possible to dismantle the electronic components from CPOLD and CPNEW samples because these compact and exceedingly small parts were intensively integrated into the base plate. In that way, for each group of samples (except for CP samples), one sample of electronic components and one sample of (bare) base plate of the WPCBs were obtained. A suffix “E” was added in brackets to all the sample labels that consisted of separated electronic components: COLD(E), CNEW(E), CRT(E), LCDCSP(E) and LCDSR(E), and to the remaining bare base plates, a suffix “B” was added in brackets: CPOLD(B), CPNEW(B), CRT(B), LCDCSP(B) and LCDSR(B).
The obtained samples were cut into plates of approximately 5 × 5 cm by using tin snips. The samples were homogenized and a mass of approximately 7 kg was separated from each sample by quartering. The reduced samples were shredded in a hammer crusher to a grain size smaller than 12 mm. Then they were quartered again to a mass of approximately 2 kg and shredded in a second step in a hammer crusher to a grain size smaller than 4 mm, as shown in Figure 2.
Schematic diagram of the carried research
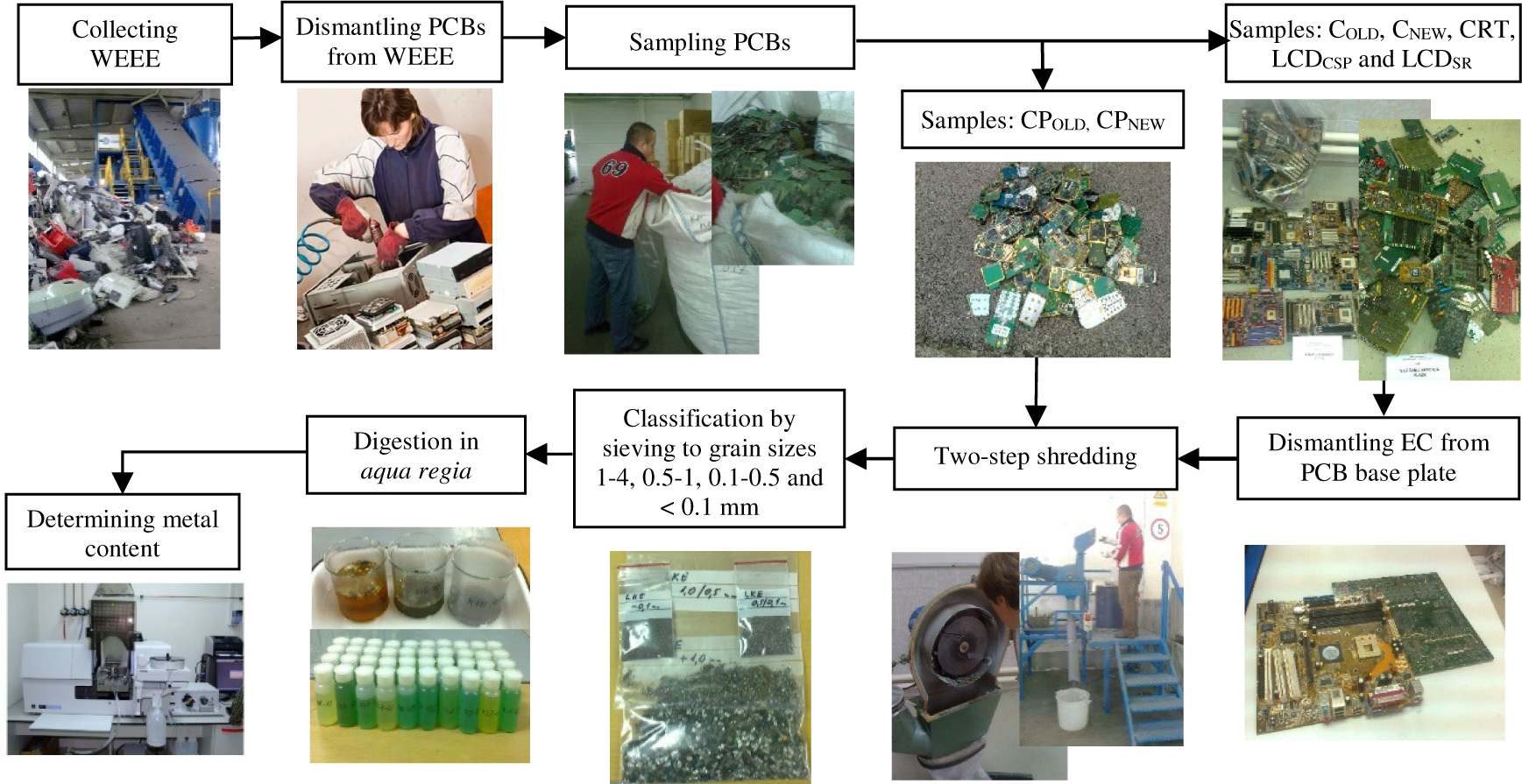
Since WPCBs were derived from different equipment with different construction, as well as different physical and mechanical properties, granulometric composition was expected to vary too. Therefore, after the second shredding step, the samples were quartered to a mass of approximately 200 g, and their granulometric composition was determined by dry sieving. The remaining part was sorted, using a laboratory sieve shaker that separated it into four grain sizes (i.e. 1-4 mm, 0.5-1 mm, 0.1-0.5 mm and < 0.1 mm) and then quartered it to a mass of approximately 50 g. The samples prepared in this way were dissolved in aqua regia(HNO3:HCl = 1:3) and their metal content was determined using an Atomic Absorption Spectrometer (AAS) Perkin Elmer AAnalyst 800, that is in the way many authors reported [25].
Mass fractions of electronic components in WPCB samples were 55.71% (COLD), 59.95% (CNEW), 85.77% (CRT), 64.97% (LCDSR) and 50.85% for (LCDCSP). These mass fractions of the electronic components were significantly higher than the data on metal content in the WPBCs published in research articles [26]. This was because the electronic components contained a large share of non-metals such as plastic, glass and ceramics. Within the aforementioned values, larger content of electronic components in the WPCBs in older models of TV sets (CRT samples) could be singled out as a result of an older technology with larger electronic components.
The efficiency of the shredding process with hammer crushers is presented by the granulometric grain size distribution curves shown in Figure 3 and Figure 4. Based on the results, it was noticed that base plate shredding was more efficient than electronic component shredding. The diagram in Figure 3 indicates that the shredding of cell phone electronic components, CPOLD(E) and CPNEW(E), was the most efficient, while the shredding of the electronic components in the case of older models of TV sets [CRT(E)] and computers of older generations [COLD(E)] was more difficult. Therefore, it can be generally concluded that the shredding efficiency of electronic components of older equipment with larger components was lower than in the case of other (new) equipment. Unlike electronic components, bare WPCBs base plates had a very similar granulometric size distribution after shredding (Figure 4), except for the samples of older models of TV sets, like CRT(B). The result can be associated with the fact that composite materials consisting of paper cloth and phenolic resin (FR2) were in the WPCBs base plates of older TV sets, while composite materials consisting of woven glass fibre and epoxy resin (FR2) were used in the new equipment.
Grain size distribution curve of shredded electronic components separated from the PCBs
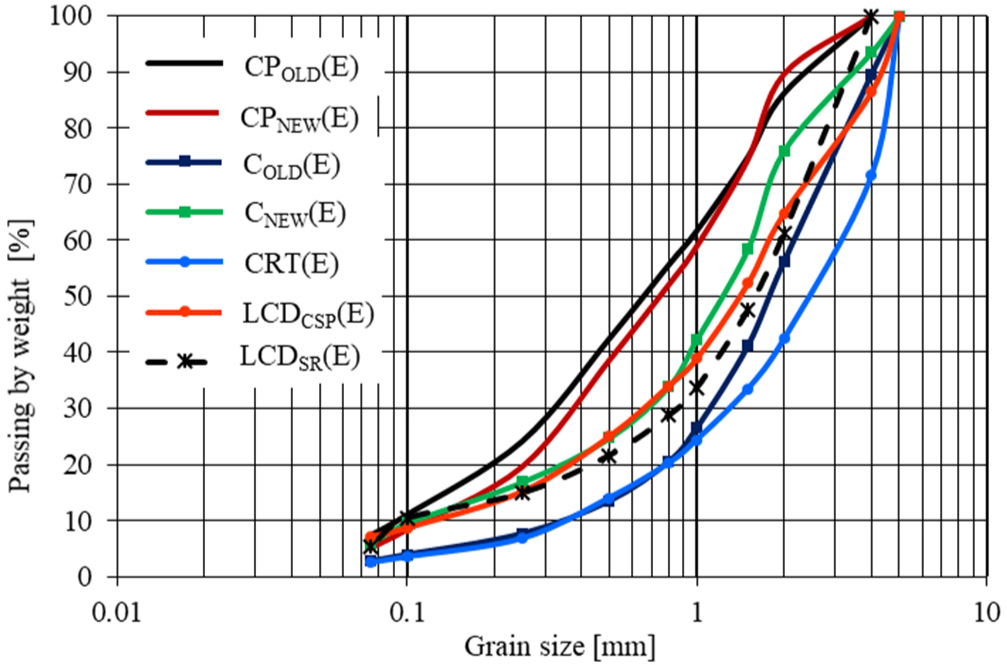
Grain size distribution of shredded bare PCB base plates
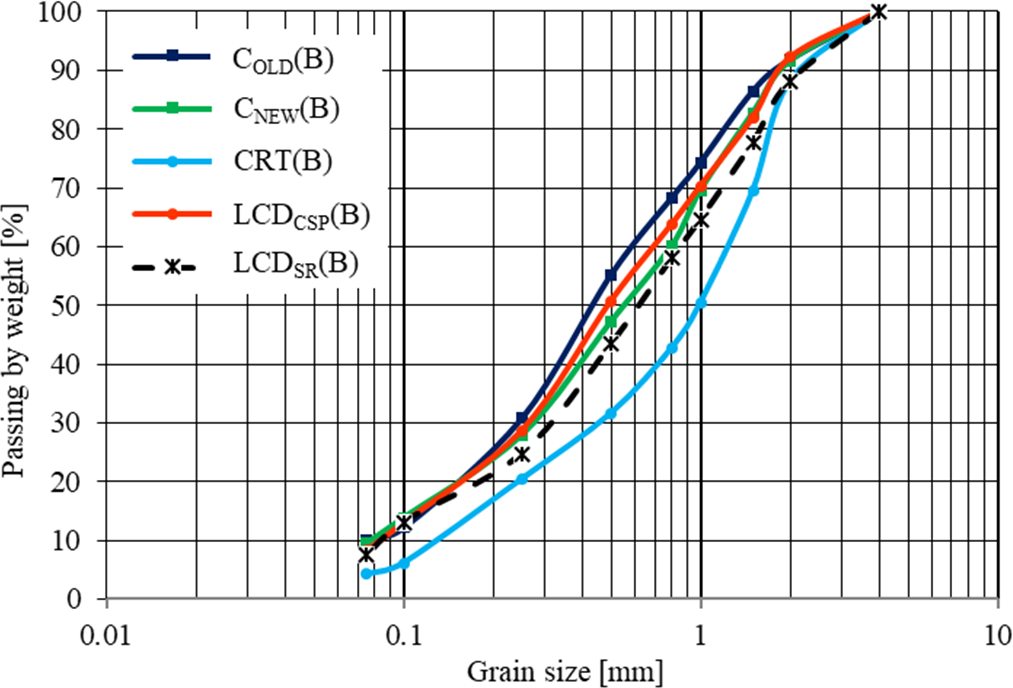
Metal content in the equipment integrated in WPCBs, depending on the type of WEEE, is shown in Table 2. The listed values were obtained by multiplying the metal content in the electronic components and bare WPCBs base plates with their mass fractions. As a result, in Table 2 the highest content of precious metals can be found in the WPCBs from equipment of higher technological level (i.e. cell phones, particularly those of newer generations). The lowest content of precious metals was present in the WPCBs of TV sets (CRT). Regarding the content of individual precious metals, it was observed that, depending on the type of equipment, the content of Au varied significantly, from 62.90 g/t (LCDSR) to as much as 1,071.96 g/t (CPNEW). On the other hand, the content of Ag was almost uniform and it did not depend significantly on the type of equipment (approximately 220 to 330 g/t, except for COLD that contained 171.05 g/t). Palladium content was the lowest and was mostly present in the WPCBs of newer cell phones (CPNEW with 61.70 g/t) and was not present at all in some WPCBs (i.e. CPOLD, CRT). Therefore, in regard to precious metal content, most of the value was present in the WPCBs of newer cell phones (CPNEW: Au content of 1,071.35 g/t, Ag of 320.10 g/t and Pd of 61.70 g/t). The lowest value was in the WPCBs from TV sets of older generations (CRT): Au content of 63.86 g/t, Ag content of 223.81 g/t and no Pd (0 g/t). In addition to precious metals, the content of a selected group of several non-ferrous metals [Al, Cu, nickel (Ni), Pb, Sn, zinc (Zn)] was determined too. For example, aluminium (Al) content ranged from 22.81 kg/t (CPOLD) to 76.47 kg/t (LCDSR). Compared to other non-ferrous metals, Cu had the highest content, ranging from 84.08 kg/t (CRT) to 428.46 kg/t (CPNEW). The content of Ni, Pb, and Sn mostly ranged from 9 kg/t to approximately 30 kg/t. Regardless of whether the results were taken from already published papers or measured during this research, all WPBCs contained Au, Ag, and Cu with mass fractions several times higher than in ores [6], [27]. The metal content of WPCBs collected in the Republic of Croatia in most cases corresponded to a wide range of published results from Table 1, and fitted recently published comparable results [28].
Table 3 presents the content of different metals in the electronic components and bare WPCB base plates of WEEE in parallel. It is evident that the metal content of Al, Cu, Ni, and Zn was higher in the electronic components, while the bare base plates had a higher content of Pb and Sn. In the case of precious metals, the investigated electronic components, in relation to the WPCBs, contained several times higher content of Au, in general a slightly higher content of Ag and a lower content of Pd, except for the COLD (E) sample. Based on the above findings, it could be observed that when separated electronic components were compared with bare WPCB base plates, the metals were mainly concentrated in the electronic components, but also bare WPCB base plates had a sufficiently high metal content to justify its further treatment. In addition to this, further treatment was also justified because WPCBs contained metals that are classified as hazardous substances.
Metal content found in WPCBs depending on the type of WEEE
Sample type | Non-ferrous metal content [kg/t] | Precious metal content [g/t] | ||||||||
---|---|---|---|---|---|---|---|---|---|---|
Al | Cu | Ni | Pb | Sn | Zn | Ʃ* | Ag | Au | Pd | |
CPOLD | 22.81 | 293.72 | 27.61 | 17.78 | 17.92 | 13.80 | 393.65 | 331.47 | 723.96 | 0.00 |
CPNEW | 29.48 | 428.46 | 31.34 | 7.32 | 26.39 | 9.38 | 532.39 | 320.10 | 1,071.35 | 61.70 |
COLD | 40.17 | 179.53 | 4.94 | 16.02 | 24.24 | 14.62 | 279.52 | 171.05 | 125.30 | 31.49 |
CNEW | 43.38 | 261.46 | 8.99 | 17.45 | 23.04 | 38.00 | 392.32 | 330.22 | 147.30 | 5.98 |
CRT | 48.41 | 84.08 | 14.22 | 13.23 | 8.33 | 14.64 | 182.91 | 223.81 | 63.86 | 0.00 |
LCDCSP | 42.98 | 264.90 | 8.69 | 12.97 | 8.48 | 11.63 | 349.66 | 321.43 | 143.76 | 7.53 |
LCDSR | 76.47 | 190.20 | 8.99 | 14.24 | 10.87 | 18.39 | 319.17 | 225.34 | 62.90 | 25.99 |
Total content of non-ferrous metals in the investigated WPCBs
Metal content in separated electronic components and bare WPCB base plates of different WEEE
Sample type | Mass fraction [%] | Non-ferrous metal content [kg/t] | Precious metal content [g/t] | |||||||
---|---|---|---|---|---|---|---|---|---|---|
Al | Cu | Ni | Pb | Sn | Zn | Ag | Au | Pd | ||
COLD(E) | 55.71 | 46.43 | 201.44 | 5.79 | 12.52 | 18.44 | 25.58 | 184.99 | 197.21 | 49.17 |
COLD(B) | 44.29 | 32.29 | 151.97 | 3.88 | 20.43 | 31.53 | 0.83 | 153.53 | 34.86 | 9.25 |
CNEW(E) | 59.95 | 47.99 | 304.87 | 11.44 | 12.83 | 11.45 | 60.88 | 340.11 | 229.17 | 2.72 |
CNEW(B) | 40.05 | 36.48 | 196.48 | 5.33 | 24.36 | 40.38 | 3.74 | 315.40 | 24.75 | 10.87 |
CRT(E) | 85.77 | 54.02 | 89.16 | 14.28 | 12.16 | 6.89 | 16.67 | 238.52 | 70.76 | 0.00 |
CRT(B) | 14.23 | 14.64 | 53.52 | 13.84 | 19.67 | 17.01 | 2.45 | 135.20 | 22.25 | 0.00 |
LCDCSP(E) | 50.85 | 63.15 | 331.33 | 10.30 | 11.03 | 7.56 | 20.17 | 350.04 | 262.19 | 5.88 |
LCDCSP(B) | 49.15 | 22.12 | 196.16 | 7.03 | 14.99 | 9.43 | 2.80 | 291.83 | 21.23 | 9.22 |
LCDSR(E) | 64.97 | 101.53 | 196.57 | 9.08 | 12.30 | 8.29 | 27.63 | 215.06 | 87.79 | 18.37 |
LCDSR(B) | 35.03 | 30.00 | 178.40 | 8.82 | 17.85 | 15.66 | 1.26 | 244.41 | 16.75 | 40.14 |
To observe the relationship between grain size and metal content, the shredded samples were sieved into four grain size fractions (1-4 mm, 0.5-1 mm, 0.1-0.5 mm and < 0.1 mm), and metal content was determined for each size separately, both for separated electronic components (Table 4), and bare PCB base plates (Table 5). Although the obtained results varied significantly for different metals, type of equipment and grain size, certain relationships could be detected.
For instance, the Al content in electronic components increased with the increase in grain size and it was the highest in the largest grain size (1-4 mm). The metal content in bare WPCB base plates and integral WPCBs of cell phones (CPOLD and CPNEW) was generally the highest in the smallest size fraction (< 0.1 mm). Copper was mostly present in larger particles, with the highest content in grain class of 0.5-1 mm in most cases. The lowest Cu content occurred in the smallest grains (< 0.1 mm), except for CRTs. This was confirmed for both electronic components as well as WPCB base plates. Therefore, it may be noticed that Cu content decreased with the decrease in the grain size of the investigated samples. Ni content was generally uniform, with no observed enrichment in a grain size, although it should be mentioned that the highest content was present in the largest grains (1-4 mm) in the case of integral cell phone WPCBs. Regarding Pb content, it was found to be the lowest in the largest grains (1-4 mm) of the shredded electronic components. However, in the case of shredded bare WPCB base plates, its concentration was significantly higher in larger grain sizes (1-4 and 0.5-1 mm) than in smaller ones (0.1-0.5 and < 0.1 mm). The Sn content in electronic components was the lowest for the largest grain size (1-4 mm) in most cases, and the highest for the grain size of 0.5-1 mm. For WPCB base plates, the metal content was generally higher for the grains of a larger size (1-4 and 0.5-1 mm), and lower for the smaller ones. For instance, Zn content in electronic components in most cases was higher for larger grain sizes and lower in smaller ones, but it was impossible to define any significant trends for WPCB base plates.
Regarding precious metals, Au was mostly present in the smallest grains, both for electronic components as well as WPCB base plates. Integral WPCBs of cell phones (CPOLD and CPNEW) were the only exception, in which the highest Au content occurred in the largest grain size fraction. Trends were not observed for the two other metals tested (i.e., Ag and Pd). It could only be stated, that in the case of Ag in the electronic components from older equipment [COLD(E) and CRT(E)], the lowest content seemed to be present in the largest grains (1-4 mm).
Pd content was below the Detection Limit (DL) in many grain sizes, both for electronic components and PCB base plates, while its content was detectable in grains of 0.5-1 mm found in CPNEW and COLD(E) samples.
Determined metal content in individual test samples of electronic components
Sampletype | Grain size [mm] | Fraction content [%] | Non-ferrous metal content per sample [kg/t] | Precious metal content per sample [g/t] | |||||||
---|---|---|---|---|---|---|---|---|---|---|---|
Al | Cu | Ni | Pb | Sn | Zn | Ag | Au | Pd | |||
CPOLD | 4-1 | 38.27 | 21.36 | 265.50 | 35.84 | 14.96 | 14.19 | 21.94 | 320.00 | 1,087.50 | < DL |
1-0.5 | 19.20 | 15.51 | 504.00 | 28.18 | 16.64 | 14.08 | 10.86 | 317.50 | 648.50 | < DL | |
0.5-0.1 | 31.47 | 22.13 | 278.20 | 18.00 | 19.12 | 19.71 | 7.64 | 300.00 | 399.00 | < DL | |
< 0.1 | 11.06 | 42.46 | 70.50 | 25.48 | 25.72 | 32.39 | 8.28 | 485.00 | 521.50 | < DL | |
CPNEW | 4-1 | 41.03 | 29.46 | 333.00 | 43.26 | 2.84 | 14.14 | 17.64 | 330.00 | 1,726.00 | < DL |
1-0.5 | 20.28 | 27.84 | 686.70 | 29.86 | 10.62 | 31.19 | 4.14 | 320.00 | 727.00 | 304.3 | |
0.5-0.1 | 30.27 | 27.61 | 487.50 | 20.98 | 11.36 | 44.23 | 3.02 | 320.00 | 501.00 | < DL | |
< 0.1 | 8.42 | 40.25 | 59.60 | 14.12 | 6.72 | 10.46 | 4.66 | 272.50 | 761.00 | < DL | |
COLD(E) | 4-1 | 73.47 | 50.92 | 178.95 | 4.40 | 8.64 | 8.56 | 23.12 | 152.50 | 154.40 | 20.11 |
1-0.5 | 13.02 | 29.02 | 399.30 | 10.94 | 27.82 | 70.50 | 37.80 | 285.00 | 254.15 | 264.25 | |
0.5-0.1 | 9.60 | 44.58 | 169.15 | 8.38 | 21.20 | 25.52 | 30.08 | 267.50 | 235.95 | < DL | |
< 0.1 | 3.91 | 24.55 | 44.50 | 8.28 | 13.14 | 13.27 | 20.18 | 260.00 | 717.50 | < DL | |
CNEW(E) | 4-1 | 57.69 | 51.25 | 387.20 | 11.42 | 7.72 | 3.09 | 65.00 | 330.00 | 221.15 | < DL |
1-0.5 | 17.53 | 40.43 | 326.20 | 12.32 | 26.74 | 39.59 | 88.05 | 387.50 | 143.85 | 0.45 | |
0.5-0.1 | 15.21 | 47.31 | 117.00 | 8.56 | 15.70 | 10.39 | 36.94 | 347.50 | 185.60 | 17.35 | |
< 0.1 | 9.57 | 43.30 | 68.00 | 14.48 | 13.64 | 12.00 | 24.36 | 302.50 | 503.00 | < DL | |
CRT(E) | 4-1 | 75.55 | 60.38 | 49.75 | 14.16 | 11.30 | 5.63 | 13.38 | 185.00 | 54.85 | < DL |
1-0.5 | 10.38 | 44.27 | 256.00 | 13.90 | 15.72 | 14.11 | 25.60 | 350.00 | 91.70 | < DL | |
0.5-0.1 | 10.55 | 28.38 | 194.75 | 14.20 | 14.00 | 6.65 | 28.40 | 325.00 | 101.40 | < DL | |
< 0.1 | 3.52 | 23.04 | 126.55 | 18.28 | 14.58 | 13.36 | 25.68 | 312.50 | 258.80 | < DL | |
LCDCSP(E) | 4-1 | 66.32 | 67.48 | 291.00 | 10.44 | 9.40 | 4.56 | 19.88 | 355.00 | 306.05 | 5.71 |
1-0.5 | 12.05 | 64.53 | 491.90 | 11.06 | 19.40 | 25.85 | 26.96 | 367.50 | 150.30 | < DL | |
0.5-0.1 | 11.27 | 51.76 | 508.20 | 9.76 | 12.12 | 7.63 | 14.88 | 327.50 | 99.30 | < DL | |
< 0.1 | 10.36 | 46.23 | 210.45 | 9.06 | 10.50 | 5.39 | 19.86 | 322.50 | 288.70 | 20.24 | |
LCDSR(E) | 4-1 | 61.08 | 106.80 | 202.45 | 8.66 | 11.06 | 8.47 | 28.78 | 207.50 | 72.65 | 29.13 |
1-0.5 | 13.89 | 102.50 | 300.70 | 10.78 | 13.72 | 15.01 | 26.34 | 220.00 | 92.80 | < DL | |
0.5-0.1 | 16.33 | 98.45 | 164.25 | 9.38 | 14.22 | 3.59 | 30.68 | 232.50 | 96.55 | < DL | |
< 0.1 | 8.70 | 68.75 | 49.60 | 8.70 | 15.14 | 5.10 | 15.86 | 227.50 | 169.70 | 6.62 |
DL = below detection limit
Considering the fact that the largest grain size (1-4 mm after shredding) had the highest mass fraction (from 38.30% to 75.55%) in relation to other grain sizes, it could be observed that the largest quantity of metals from electronic components could be recovered by treating large size (1-4 mm) grains. When bare base plates were taken into consideration, it was obvious that the smallest grain size (of < 0.1 mm) had the lowest mass fraction, and that the mass fraction of a larger grain size (of 0.5-1 mm) was approximately 20%. The highest mass fraction in the shredded PCB base plates was present both in the largest grain size: 1-4 mm (from 25.66% to 49.50%), and in the smallest grain size of 0.1-0.5 mm (from 25.52% to 43.04%), respectively.
Metal content in the individual tested samples of bare WPCB base plates
Sample type | Grain size [mm] | Fraction content [%] | Non-ferrous metal content per sample [kg/t] | Precious metal content per sample [g/t] | |||||||
---|---|---|---|---|---|---|---|---|---|---|---|
Al | Cu | Ni | Pb | Sn | Zn | Ag | Au | Pd | |||
COLD(B) | 4-1 | 25.66 | 23.00 | 232.00 | 4.14 | 33.66 | 65.35 | 0.74 | 140.00 | 47.25 | < DL |
1-0.5 | 19.11 | 30.62 | 290.00 | 4.44 | 41.12 | 68.50 | 0.92 | 235.00 | 42.05 | 40.35 | |
0.5-0.1 | 43.04 | 35.73 | 82.67 | 3.62 | 6.96 | 3.12 | 0.70 | 125.00 | 22.35 | < DL | |
< 0.1 | 12.19 | 42.28 | 11.90 | 3.34 | 7.68 | 2.71 | 1.32 | 155.00 | 41.65 | 12.63 | |
CNEW(B) | 4-1 | 30.44 | 34.76 | 257.60 | 5.48 | 39.48 | 78.37 | 6.44 | 262.50 | 19.95 | 12.48 |
1-0.5 | 22.34 | 33.23 | 300.47 | 5.60 | 36.72 | 62.61 | 4.56 | 365.00 | 22.70 | 3.20 | |
0.5-0.1 | 33.43 | 35.87 | 148.67 | 5.32 | 9.20 | 6.16 | 1.62 | 327.50 | 21.55 | 19.02 | |
< 0.1 | 13.79 | 47.02 | 9.13 | 4.56 | 7.70 | 3.47 | 1.60 | 322.50 | 46.40 | < DL | |
CRT(B) | 4-1 | 49.50 | 4.90 | 67.47 | 14.04 | 32.40 | 28.85 | 1.90 | 157.50 | 17.53 | < DL |
1-0.5 | 18.82 | 7.97 | 55.33 | 13.66 | 9.78 | 7.64 | 1.20 | 95.00 | 19.60 | < DL | |
0.5-0.1 | 25.52 | 30.24 | 33.63 | 13.70 | 5.72 | 3.08 | 3.88 | 115.00 | 24.20 | < DL | |
< 0.1 | 6.16 | 48.67 | 18.25 | 13.34 | 5.34 | 8.28 | 4.80 | 162.50 | 60.15 | < DL | |
LCDCSP(B) | 4-1 | 35.34 | 18.74 | 268.20 | 7.14 | 14.96 | 17.63 | 2.44 | 327.50 | 12.60 | 3.89 |
1-0.5 | 21.29 | 22.27 | 269.67 | 6.74 | 24.30 | 10.75 | 4.70 | 385.00 | 28.90 | 36.87 | |
0.5-0.1 | 30.32 | 17.96 | 136.00 | 7.16 | 10.36 | 2.43 | 1.82 | 205.00 | 9.05 | < DL | |
< 0.1 | 13.05 | 40.66 | 21.00 | 6.88 | 10.64 | 1.37 | 2.98 | 245.00 | 60.35 | < DL | |
LCDSR(B) | 4-1 | 29.67 | 18.31 | 282.00 | 9.44 | 23.54 | 29.04 | 0.48 | 270.00 | 14.60 | 66.27 |
1-0.5 | 19.56 | 17.17 | 310.00 | 9.16 | 22.00 | 20.56 | 1.54 | 240.00 | 13.53 | 15.97 | |
0.5-0.1 | 37.85 | 43.30 | 85.50 | 8.58 | 13.34 | 6.84 | 1.82 | 272.50 | 17.50 | 45.85 | |
< 0.1 | 12.92 | 37.28 | 13.30 | 7.62 | 11.68 | 3.36 | 0.98 | 110.00 | 24.38 | < DL |
DL = below detection limit
When mass fractions of metals in WPCBs from newer and older WEEE were compared, the relationship between mass fraction and age (the development of technology) became evident. Figure 5 presents the mass fraction ratio of individual metals determined in newer and older waste PCBs from three different types of equipment.
The figure shows that Au, Sn, Cu, Al and Ni were more frequently used in the WPCBs of newer cell phones (CPNEW), while Zn and Pb content was less frequently used.
When the ratios of mass fractions of metals in the WPCBs from computers were compared, an increase in the use of Zn, Ag, Ni, Cu and Au could be observed, while the use of Al, Pb, and Sn remained at almost the same level. The use of Pd in newer computers significantly decreased when compared to older models.
Data on the metal content in LCD TV sets represented an arithmetic mean of a metal content in LCDCSP and LCDSR. If the data obtained for TV sets are considered, one can observe a significant increase in the use of Cu, Au, Ag, Al and Sn, but Ni was used less frequently, while Pb and Zn mostly remained at the same level. The reason for a negligible decrease of Zn and Pb content in newer equipment was due to the fact that the share of WEEE treated in the Republic of Croatia according to the RoHS Directive was small, and changes may be expected in the future when products begin to reach their end-of-life.
Metal mass fraction ratio in waste PCBs in relation to equipment age and type
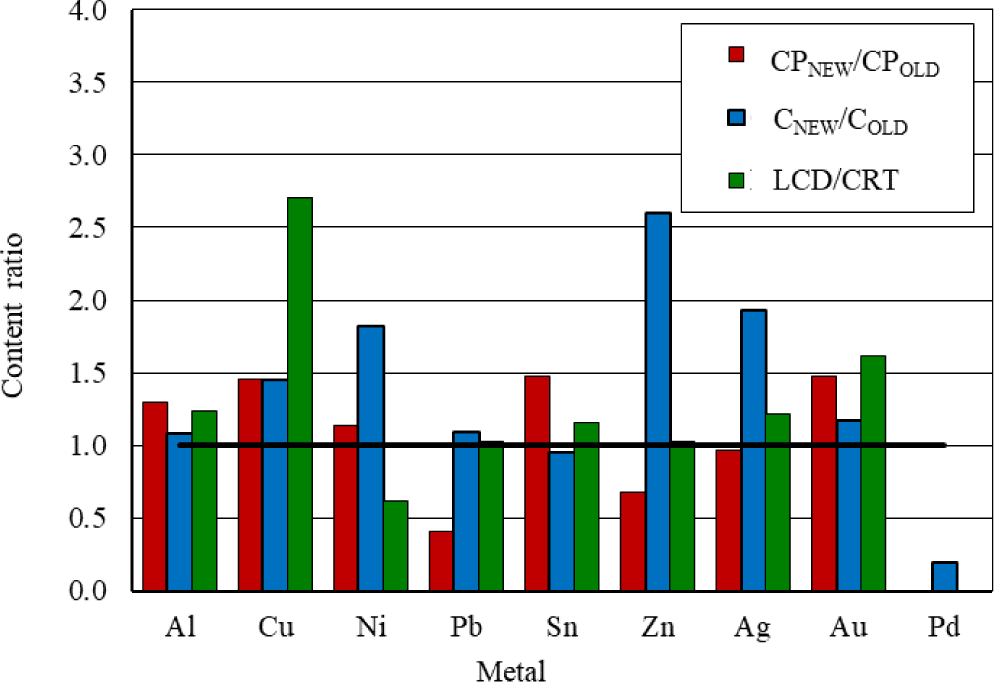
The research presented in this paper shows that the mass of electronic components in WEEE represented a larger part than the mass of integral WPCBs, and that the mass fraction of electronic components depended significantly on the age and type of WEEE. Depending on the type of equipment, the mass fraction of electronic components ranged from 50.85% (LCDCSP) to 85.77% in the case of older TV sets (CRT).
Based on the granulometric particle size distribution of samples determined after a two-step shredding, it was observed that the efficiency of WPCB base plates shredding was higher than for electronic component shredding. The shredded WPCB base plates from different WEEE had similar particle size distributions. In the case of electronic components, it was easier to shred the components from cell phones and more difficult to shred those from older TV sets.
The comparison of the determined metal content in separated electronic components and WPCB base plates showed that a higher metal content (Al, Cu, Ni, Zn, Au, and Ag in most cases) could be found in electronic components rather than in bare WPCB base plates. The opposite was true for certain metals, i.e. Pb, which had a higher content in WPCB base plates than in electronic components. Moreover, in the case of some metals (e.g. Pd and partly true for Ag), the metal content depended on the type of equipment.
The research on the relationship between metal content and grains of various size showed uneven results. The shredded electronic components of larger grain sizes (1-4 mm and 0.5-1 mm) contained more Al, Cu and Zn but the least amount of Pb. The smaller grain sizes of electronic components, on the other hand, contained more Au. The larger grain sizes of shredded PCB base plates contained more Cu, Pb and Sn, but grains of the smallest size (< 0.1 mm) contained more Al and Au. The content of Ni was rather uniform, and it could be concluded that its concentration generally did not relate to any grain size. No trends were noticed for Ag and Pd also.
Considering that, after shredding of the electronic components, the largest grain size (1-4 mm) also had the largest mass fraction when compared to the other three grain sizes fractions. Thus, its treatment will result in the highest metal recovery. After the shredding of WPCB base plates, grains of 1-4 mm and of 0.1-0.5 mm had the largest mass fractions, respectively.
The conducted research also indicates certain trends in the use of metals in PCBs depending on the product’s age. It can be concluded that an increase in the use of Al, Cu, and Ag occurred in most of the new equipment. Metals such as Sn and Pb were used almost equally in all the equipment, regardless of the product’s age. A significant increase of Pd in newer TV sets was observed, as well as a significant decrease of Pd in newer computers.
Our research showed that WPCBs contained several strategic metals in concentrations several times higher than in ores. The separation of electronic components from WPCB base plates by segregation resulted in a higher concentration of metals in those components. Nevertheless, in bare WPCB base plates there were enough metals left for further treatment from an economic point of view, as well as from an environmental point of view, which means less waste toxicity.
Abbreviations | |
---|---|
AAS | Atomic Absorption Spectrometer |
CNEW | Computers Newer Generation Processors (computers with processor Pentium 5 or newer) |
COLD | Computers Older Generation (computers with Pentium 4 processor or older) |
CP | Cell Phones |
CPNEW | Cell Phones New Generation (smartphones manufactured after 2008) |
CPOLD | Cell Phones Older Generation |
CRT | Cathode Ray Tube |
CV | Coefficient of Variation |
EE | Electrical and Electronic |
EEE | Electrical and Electronic Equipment |
FR2 | Flame Resistant 2 (PCB base plate made of phenolic resin bonded paper) |
FR4 | Flame Resistant 4 (PCB base plate made of woven fiberglass cloth with an epoxy resin binder) |
LCD | Liquid Crystal Display |
LCDCSP | Liquid Crystal Display Computer Signal Processing Unit |
LCDSR | Liquid Crystal Display Computer Signal Reception Unit |
PCB | Printed Circuit Board |
SD | Standard Deviation |
TV | Television |
USD | United States Dollar |
WEEE | Waste Electrical and Electronic Equipment |
X̄ | Mean |
Recycling of Waste Printed Circuit Boards: A Review of Current Technologies and Treatment Status in China ,Journal of Hazardous Materials , Vol. 164 (2-3),pp 399-408 , 2009, https://doi.org/https://doi.org/10.1016/j.jhazmat.2008.08.051
, Dynamic Visualisation of Municipal Waste Management Performance in the EU Using Ternary Diagram Method ,Waste Management , Vol. 61 ,pp 558-571 , 2017, https://doi.org/https://doi.org/10.1016/j.wasman.2017.01.018
, How Are WEEE Doing? A Global Review of the Management of Electrical and Electronic Wastes ,Waste Management , Vol. 31 (4),pp 714-730 , 2011, https://doi.org/https://doi.org/10.1016/j.wasman.2010.10.023
, Current Status and Future Perspective of Recycling Copper by Hydrometallurgy from Waste Printed Circuit Boards ,Procedia Environmental Sciences , Vol. 31 ,pp 162-170 , 2016, https://doi.org/https://doi.org/10.1016/j.proenv.2016.02.022
, Potential Phytoremediator of Native Species in Soils Contaminated by Heavy Metals in the Garbage Dump Quitasol-Imponeda Abancay ,Journal of Sustainable Development of Energy, Water and Environment Systems , Vol. 7 (4),pp 584-600 , 2019, https://doi.org/https://doi.org/10.13044/j.sdewes.d7.0261
, - , Countering Illegal Traffic: A Snapshot of Monitoring and Enforcement in Waste Crime – Waste Risks: Gaps in Meeting the Global Waste Challenge, A UNEP Rapid Response Assessment, United Nations Environment Programme and GRID-Arendal, Nairobi and Arendal, 2015
Novel Application of the Nonmetallic Fraction of the Recycled Printed Circuit Boards as a Toxic Heavy Metal Adsorbent ,Journal of Hazardous Materials , Vol. 252-253 ,pp 166-170 , 2013, https://doi.org/https://doi.org/10.1016/j.jhazmat.2013.02.037
, Recovery of Waste Printed Circuit Boards Through Pyrometallurgical Processing: A Review ,Resources, Conservation and Recycling , Vol. 126 ,pp 209-218 , 2017, https://doi.org/https://doi.org/10.1016/j.resconrec.2017.08.001
, Precious Metals Recovery from Waste Printed Circuit Boards: A Review for Current Status and Perspective ,Resources, Conservation and Recycling , Vol. 113 ,pp 28-39 , 2016, https://doi.org/https://doi.org/10.1016/j.resconrec.2016.05.007
, Environmental Impacts and Benefits of State-Of-The-Art Technologies for E-Waste Management ,Waste Management , Vol. 68 ,pp 458-474 , 2017, https://doi.org/https://doi.org/10.1016/j.wasman.2017.06.038
, Toxic Metals in WEEE: Characterization and Substance Flow Analysis in Waste Treatment Processes ,Science of the Total Environment , Vol. 463-464 ,pp 1124-1132 , 2013, https://doi.org/https://doi.org/10.1016/j.scitotenv.2012.07.078
, The Major Components of Particles Emitted During Recycling of Waste Printed Circuit Boards in a Typical E-Waste Workshop of South China ,Atmospheric Environment , Vol. 44 (35),pp 4440-4445 , 2010, https://doi.org/https://doi.org/10.1016/j.atmosenv.2010.07.040
, - , Characterisation of Computer Printed Circuit Boards for Hazardous Properties and Beneficiation Studies, Proceedings of the XXV International Mineral Processing Congress, 2010
The Status and Development of Treatment Techniques of Typical Waste Electrical and Electronic Equipment in China: A Review ,Waste Management and Reseach , Vol. 32 ,pp 254-269 , 2014, https://doi.org/https://doi.org/10.1177/0734242X14525824
, Model for Regional Management of Electrical and Electronical Waste (WEEE) Flows ,Environmental Engineering and Management Journal , Vol. 17 (1),pp 135-145 , 2018, https://doi.org/https://doi.org/10.30638/eemj.2018.015
, The Possibility of Using Non-Metal Fraction from Printed Circuit Boards in Pavement Manufacturing ,Environmental Engineering and Management Journal , Vol. 17 (11),pp 2719-2729 , 2018
, Current Status and Future Perspective of Waste Printed Circuit Boards Recycling ,Procedia Environmental Sciences , Vol. 16 ,pp 590-597 , 2012, https://doi.org/https://doi.org/10.1016/j.proenv.2012.10.081
, Separation of the Metallic and Non-Metallic Fraction from Printed Circuit Boards Employing Green Technology ,Journal of Hazardous Materials , Vol. 311 ,pp 91-99 , 2016, https://doi.org/https://doi.org/10.1016/j.jhazmat.2016.02.061
, The Possibility for Environmental Friendly Recycling of Printed Circuit Boards ,Journal of Sustainable Development of Energy, Water and Environment Systems , Vol. 4 (1),pp 14-22 , 2016, https://doi.org/https://doi.org/10.13044/j.sdewes.2016.04.0002
, Characterization of the Non-Metal Fraction of the Processed Waste Printed Circuit Boards ,Waste Management , Vol. 95 ,pp 94-102 , 2018, https://doi.org/https://doi.org/10.1016/j.wasman.2018.02.010
, Prioritizing Material Recovery for End-Of-Life Printed Circuit Boards ,Waste Management , Vol. 32 (10),pp 1903-1913 , 2012, https://doi.org/https://doi.org/10.1016/j.wasman.2012.05.005
, - , Recovery of Waste Printed Circuit Boards Using Mineral Processing Methods, Ph. D. Thesis, 2016
Innovative Technologies for Metals Recovery and Plastic Valorization from Electric and Electronic Waste: An Integrated Approach ,Environmental Engineering and Management Journal , Vol. 14 (7),pp 1553-1562 , 2015, https://doi.org/https://doi.org/10.30638/eemj.2015.167
, - , , A Report on Special Categories of Waste for 2016 (in Croatian), 2018
Characterization and Recovery of Polymers from Mobile Phone Scrap ,Waste Management and Research , Vol. 29 (7),pp 714-726 , 2011, https://doi.org/https://doi.org/10.1177/0734242X10391528
, Evaluating Waste Printed Circuit Boards Recycling: Opportunities and Challenges, A Mini Review ,Waste Management and Research , Vol. 35 (4),pp 346-356 , 2017, https://doi.org/https://doi.org/10.1177/0734242X16682607
, Aqueous Metal Recovery Techniques from E-Scrap: Hydrometallurgy in Recycling ,Minerals Engineering , Vol. 25 (1),pp 28-37 , 2012, https://doi.org/https://doi.org/10.1016/j.mineng.2011.09.019
, Analysis of the Metal Content of Small-Size Waste Electric and Electronic Equipment (WEEE) Printed Circuit Boards—Part 1: Internet Routers, Mobile Phones and Smartphones ,Resources, Conservation and Recycling , Vol. 133 ,pp 300-308 , 2017, https://doi.org/https://doi.org/10.1016/j.resconrec.2017.02.011
,